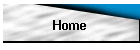
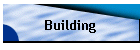
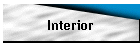
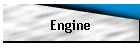
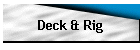
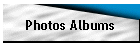
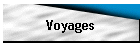
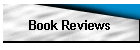
| |
Building and Sailing Thlaloca
Dos

Before
the start of any building process many preliminaries have to be considered
with great thought.
In this regard it is past experience which helps immeasurably to arrive at some
conclusion faster than anyone with none. This, of course, is fundamental to
anyone faced with any task.
In
our case there were several basic requirements, not necessary in the order
presented:
Now
to the nitty-gritty's:
As
a builder in love with wood, creating our future craft in wood was the only
material I felt comfortable with. In considering the type of planking, I
concluded that cold-molded assured us being the lightest but strongest hull
sheeting, outside of metal. In this type of construction, the scantlings are
bend over a "network" of longitudinal stringers spaced appropriately.
Now, these individual stringers are potential water traps and cause rot. A much
better solution is strip-planking the first layer. The advantage is a smooth
inner hull, and a good foundation to fasten the diagonals--the second
layer. As a bonding agent between layers we used epoxy glue and monel ring-nails
as fasteners throughout. The third layer is carvel, why? Because no matter how
careful the outer layer is finished, the normal contraction and expansion of
wood will show under certain light condition even through two layers of Vectra
cloth, we put as final layers for additional strength, and guarding against
water absorption and worms. Meaning to say that carvel appearance is more the
natural print and less obtrusive. Also, having strip planking as the inner
layer, the outer layer of carvel makes matching seems less likely. To make
absolutely certain there will not be any moisture penetration, we bonded
the last layer with polysulphide to one foot above the waterline. The
thickness of the individual layers are: Strip planking 1-1/8", diagonals
1/4", carvel 3/8" There are 10 full or partial bulkheads. One thing
about Vectra cloth it is very strong, and compared to fiberglass superior
in strength and abrasion resistance. It is perfectly alright to use polyester
resin for bonding, but the real advantage of Vectra is gained by using epoxy
resin. Because polyester brittles with time whereas epoxy retains elasticity. We
don't have a single failure after 26 years. But nothing is perfect. Vectra is a
"bitch" to finish; and can only be accomplished by way of
careful sanding. Because, once a mechanical sander hits the cloth it sort of
melts and fusses and the only way to repair it is by applying more epoxy filler.
In short, from the outset, the hull should be pasted with a thick layer of
fairing compound, epoxy in our case, in order to have enough "meat" to
prevent cut-ins. The hull was built upside down, therefore provided the huge
advantage not having to "pump iron" (sanding overhead). This type of
hull construction is labor intensive, and building up-side-down is the only way
to lighten the load significantly. Nice would be a roller contraption used
primarily in steel construction, that would facilitate easy building and
handling of the hull immensely. But, like everything else in life, there are
trade-offs; and in boat building particularly so.


Homepage
Interior
|